News & Events
Blog post: Additive manufacturing: at the core of efficient and sustainability in rail repairs
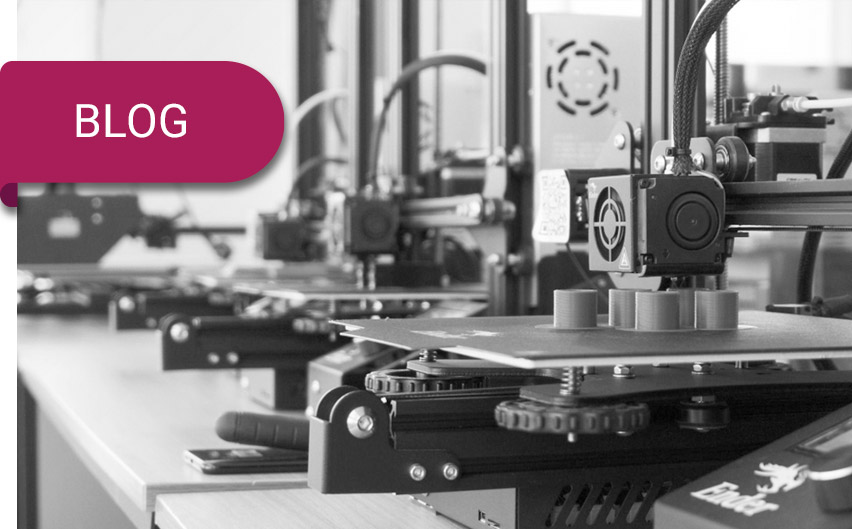
13 | 12 | 2022
The incorporation of new smart, digital materials and technologies into the means and systems of production has enabled the industry to evolve towards a concept of advanced manufacturing that is capable of providing added value to numerous sectors such as transport and capital goods.
In this regard, advanced manufacturing involves a production system that absorbs the potentialities and resources of Industry 4.0 to optimise products and processes and increase efficiency and sustainability within the area of production. This system is founded on four pillars that sustain the process’s entire value chain.
Pillars of advanced manufacturing
Materials
Advanced manufacturing brings together state-of-the-art materials with a view to providing solutions with greater added value or to improving certain processes.
Means
Uses innovative production tools and products.
Manufacturing processes
Optimises production processes in order to increase efficiency and sustainability.
Systems
Backed up by tools based on electronics, information and communications technologies (EICTs), so as to lend support to the entire value chain.
Within this production system, additive manufacturing provides major opportunities for increasing efficiency and profitability of certain sectors such as rail. In Europe alone, estimated maintenance cost for the rail system as a whole exceeds 10,000 million Euros annually, broken down into around 300 areas responsible for infrastructures, rail operators and integrated operators.
Maintenance decisions regarding vehicles and rail infrastructure are taken separately and are based on periodic inspections to determine the state of a component in terms of certain parameters.
For their part, maintenance tasks are performed when certain warning thresholds have been exceeded, albeit before this goes beyond safety conditions. Within these maintenance tasks, it is crucial to prolong rail lifespan to the maximum from a financial standpoint, given that its renewal entails around 40% of the construction cost of each kilometre of rail track. This cost makes it essential to optimise maintenance work to the maximum and, above all, carry out repairs on rails and railway crossings as swiftly, sustainably and effectively as possible.
Profitable and efficient alternative to rail repairs
An innovative additive manufacturing system has emerged in recent times known as Laser Metal Deposition (LMD), a type of technology that enables repairs to rail and railway crossings, among others, to be made more sustainably and efficiently. This is founded on three basic principles:
-
This is an emergent technology applicable to rail repairs.
-
Integrating state-of-the-art materials: additive manufacturing uses metal powders of between 45 and 100 micra. CEIT conducts research into different materials in order to perform these repair tasks on rails and crossings.
-
The process is based on efficiency and sustainability. In situ repairs to rails and crossings are more efficient and sustainable than replacing the damaged section, because it avoids the energy expense that producing a new component and transporting it to the place of repair entails.
This technology provides a range of advantages over other types of welding such as manual welding, manual metal arc (MMA) and aluminothermic welding.
On the one hand, it ensures better metallurgical properties than welding because it enables the main parameters of the process to be accurately varied and the metallurgical properties of the repaired area controlled.
On the other, it enables the Heat Affected Zone (HAZ) to be controlled accurately and ensures controlled dilution between the material provided and the component to be repaired or substrate. Either very small dilutions (less than 3%) can be obtained, or very large ones if required, and no moulds or tools are needed.
All the above reasons make additive manufacturing using LMD technology a good option for rail repairs in terms of sustainability, efficiency and profitability.
For more information, you can download our free ebook about railroads: