Thermomechanical Processing
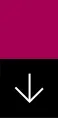
Our added value
A long history offering the best support to companies in the steel sector supports us. Our researchers carry out projects aimed at expanding knowledge, promoting technical advances and process improvements that contribute to obtaining more advanced products in a more sustainable way.
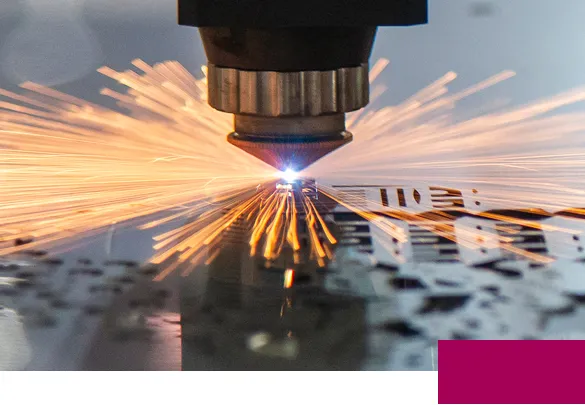
Our research lines
In addition, the research carried out by the area contributes to the training of young researchers. The result obtained in these fundamentally basic research projects represents the starting point for solving specific problems posed in the more complex projects that our clients send us.
New processing routes and improvements in processing sequences for flat and long products, tubes, forged pieces, etc.
Semi-finished products, thin slab casting, direct rolling.
Improvements to heat and thermomechanical treatments and new solutions based on them.
Composition optimization.
Zero-defect production.
Designed-to-order alloys with improvements to specific properties.
New ranges of high-strength steels.
Advanced microalloyed steels.
Projects
The basic research carried out by the Group over the past six years is defined by the following projects:
BAICONFORM
Advanced High Strength Steels (AHSS), bainite, microstructure, mechanical properties, formability, modeling
Read moreAUSTOUGH
Austenite reconstruction tool for low-temperature toughness control in heavy gauge steels
Read moreOPTIBOS
New developments and optimisation of high strength boron treated steels through the application of advanced boron monitoring techniques
Read morePRETICONTROL
Control of precipitation sequences during hot rolling to improve product uniformity of titanium containing high strength steels
Read moreVIRTROLL
Development of metallurgical bases for numerical simulation of lamination processes based on flexible design
Read moreETHPRIN
Extensión de Nuevas Tecnologías y Herramientas de Digitalización para la Producción Inteligente de Componentes para Entornos Hostiles
Read more