Additive manufacturing
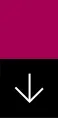
At Ceit, we specialize in every stage of additive manufacturing and powder metallurgy. We develop comprehensive solutions that cover everything from the research and development of new materials in the form of metallic or ceramic powders, to the optimization of advanced processes using state-of-the-art technologies. Our expertise spans both additive techniques and conventional powder consolidation processes, enabling us to design solutions tailored to the functional, mechanical, and economic requirements of each client.
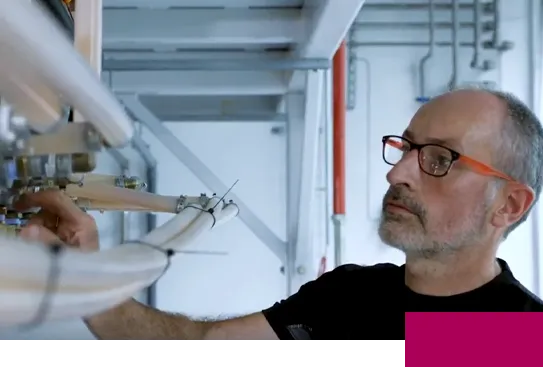
Solutions
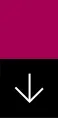
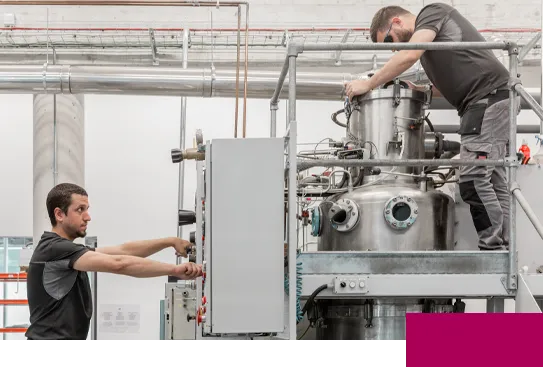
Powder atomisation
The additive manufacturing process starts with the selection and preparation of high- quality materials. At Ceit we have an atomisation pilot plant at our disposal that enables us to develop customised metal powders with particle size distribution (PSD and D50) that meet the specific requirements of each application. These materials, which are free of any defects and are highly recyclable, guarantee optimum performance at any part of the additive process.
Más información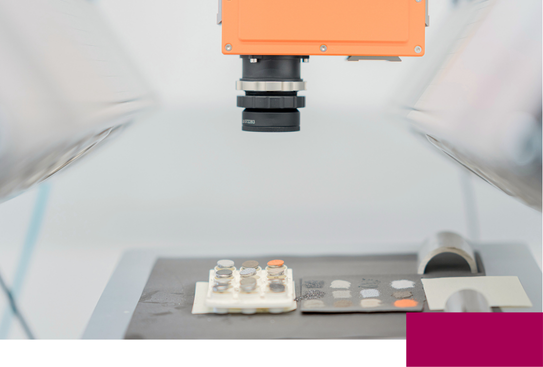
Topology optimisation
Topology atomisation is a key tool in maximising the benefits of additive manufacturing. We design lighter, more efficient parts using advanced computational algorithms, thus reducing the use of material (without compromising structural resistance).
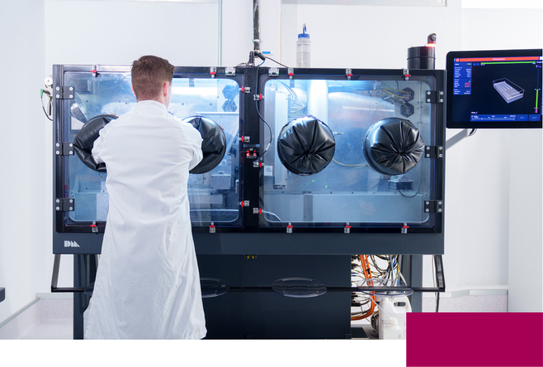
Binder jetting
We use Binder Jetting technology for applications requiring productivity and precision in manufacturing. This process is known for its versatility in producing complex parts with metallic and ceramic materials. Binder Jetting stands out for its scalable production capacity, balancing customization and efficiency.
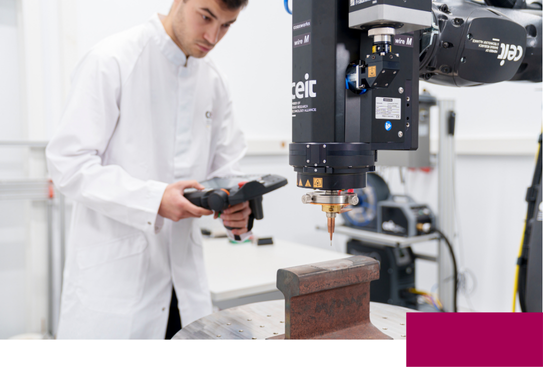
Laser directed energy deposition (L-DED)
We integrate laser directed energy deposition (L-DED) as a key technology in the manufacture and repair of components of all sizes. This process uses high-precision lasers to melt materials in powdered or threaded format, providing customised solutions with exceptional mechanical properties.
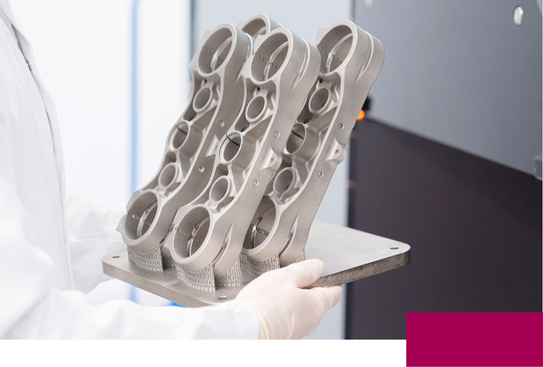
Powder bed fusión laser beam (PBF-LB)
The powder bed fusion (PBF) process combines precision and versatility in the manufacture of parts with complex geometries vis selective laser fusion. This technology ensures the utmost precision and versatility in terms of manufacture, enabling components with greater mechanical and dimensional properties to be developed.
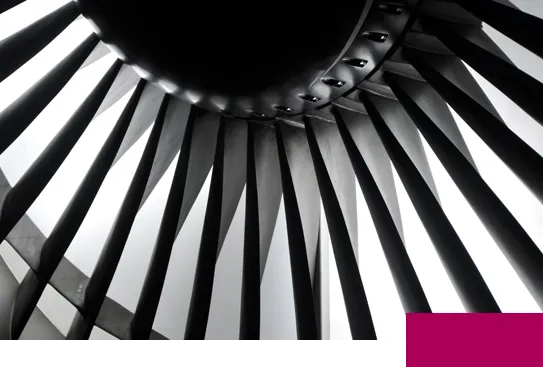
Hot isostatic pressing (HIP)
We enhance the structural integrity of metallic and ceramic components through Hot Isostatic Pressing (HIP), a technology based on the simultaneous application of high temperature and isostatic pressure. This process eliminates porosity, increases density, and optimises the mechanical properties of critical parts. We apply HIP both for the consolidation of encapsulated powders—achieving near-net-shape components or ingots for forging and rolling—and for diffusion bonding of similar or dissimilar materials.
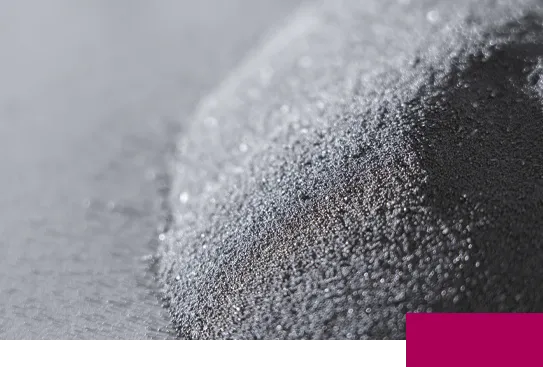
Power metallurgy processes
Development and optimization of powder metallurgy processes, with proven expertise in uniaxial pressing —both cold and hot— and sintering. These technologies are essential for manufacturing magnetic materials, hardmetals, and refractory components. Activities range from the design of new material grades to experimental validation under real operating conditions, enabling tailored solutions that enhance component density, strength, and functional properties. In addition, specific stages of Metal Injection Molding (MIM) are addressed —mainly material development and partial validation— although it is not a core activity.