Forging
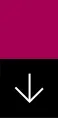
The forging industry is facing the challenge of manufacturing increasingly demanding components in terms of mechanical performance features, energy efficiency and sustainability. From the development of special steels and advanced alloys to the optimisation of hot deformation processes via simulation and modelling, our capacities cover all stages in the manufacturing process by integrating advanced digital tools. By using a continuous improvement-based approach, we provide solutions to enable operative efficiency to be optimised, faults reduced, and advances made towards manufacturing more sustainable models.
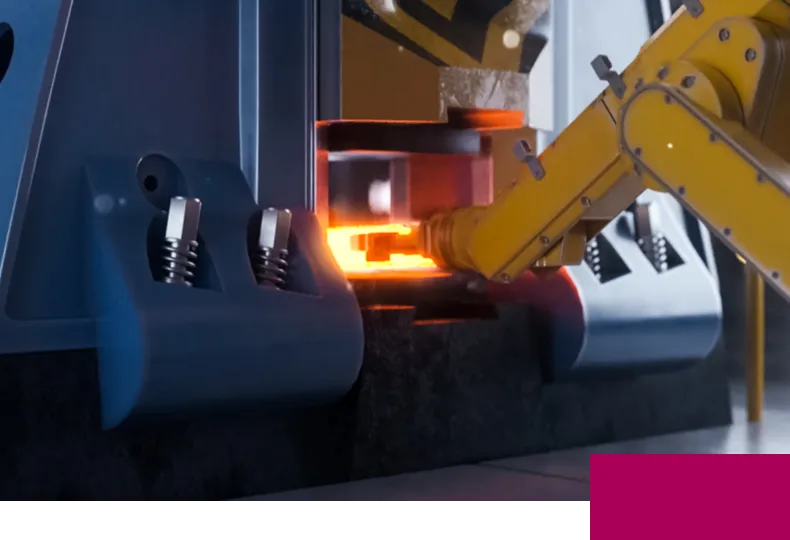
Capacities
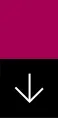
Advanced materials
We design and characterise customised special steels (medium/high carbon, with high/low alloys, microalloys, stainless, etc.) and superalloys (Fe and Ni-based) adapted to forging process demands. These developments enable the components’ mechanical properties to be improved, their lifespan increased, and also environmental impact reduced.
Further informationSteel forming
We optimise processes such as hot forming, using simulation tools – finite commercial elements and our own programmes – and numerical modelling, which enable the material’s behaviour to be predicted, the deformation flow assessed, and faults prevented. We research into new ranges of sustainable steels with high added value, as well as steels adapted to the hydrogen economy. Additionally, we generate specific material and process models with which we then develop software for the design and validation of the forging process.
Further informationZero-defect manufacturing
We analyse any deviations and non-conformities that may emerge in the course of the different forming stages. As a result, we define the optimum manufacturing roadmap to prevent faults and minimise the loss of material. We specialise in the development of contactless parts inspection techniques via the use of electromagnetic techniques, artificial intelligence algorithms and optical image processing, in order to detect any surface defects and ensure dimensional control.
Further informationAdditive manufacturing and powder metallurgy
We complement conventional forging processes with additive manufacturing processes such as L-DED for the repair and hybrid manufacturing of components and moulds, and also with special thermal treatments such as hot isostatic pressing (HIP), in order to improve the material’s density and resistance.
Further informationSmart factory
We integrate advanced technologies with a view to automating and digitalising forging processes and those involving subsequent thermal treatments. From collaborative robotics and operator assistance to real-time monitoring, localisation systems, inspection and digital twins, our solutions allow for total control over the process and a substantial improvement in productivity in secure, connected environments.
Further information